For more than 20 years, the patented Excel Modular Scaffold System has been the premier scaffolding system in the
market, offering many benefits and advantages over other types of system scaffolding. When a petrochemical company was performing expansion and maintenance of an ethylene unit at its complex in the Gulf Coast, the company chose the Excel system for scaffold decking of a C2 Splitter.
Maintenance is performed on a C2 Splitter during a turnaround to improve operating efficiencies, increase equipment service life and reduce the number of costly equipment replacements. Gallop Tower Field Services and Century Elevators also worked collaboratively with Excel on the C2 Splitter structure but each company carried a different scope of work.
“Everyone on this job performed efficiently and nobody got hurt.”
— Chad King, Excel Modular Scaffold

While Gallop oversaw the logistics on site during the turnaround, Century Elevators installed a dual car elevator system rated at 6,000 pounds capacity and was able to hold 30 men per car. Century provided vertical transportation to seven landing levels on the splitter to assist with turnaround activities being performed simultaneously on all levels. The purpose was to transport the material components required for the operation and to move more than 2,500 personnel at any given time during the 24-hour a day process.
Excel provided the scaffold decking with access for the tray installation that also supported the elevators and alternate access. The Excel scaffold had to support large capacity loads of up to 6,000 pounds on each deck for installation of new trays and other components on the unit. “The whole purpose of the scaffold and elevator structure was to save crane time,” said Chad King, vice president of operations for Excel Modular Scaffold. “We put a lot of emphasis on the planning side and our manufacturer, Deltak Manufacturing, was able to fabricate components that would distribute the weight of everything. Execution went flawlessly on this project.” The Excel scaffold had to reach a height of more than 260 feet with the top 230 feet of scaffold allowing a load of 8,700 pounds per leg. The lower part of the scaffold had to be built with shoring legs with allowable loads of 37,500 pounds per leg.
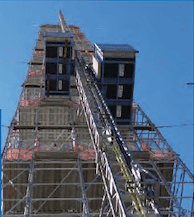

All of this was performed without ever making contact with the splitter structure itself. “Excel was chosen for this project because we have a unique industrial scaffold system that is stronger and we have the engineering capabilities to complete a project of this magnitude,” King said. “The scaffold was paramount as far as logistics were concerned because the complex had a major turnaround going on. The engineering of the Excel scaffold allows it to take so much more of a load. We used computerized drawings to model the scaffold to the right specifications. During the project, we didn’t have to move a single component of the scaffold, which speaks highly of Excel’s engineering.” The elevator and scaffolding were braced every 29 feet vertically by way of beams and custom struts. The elevator tie-in system distributed the loads back through the scaffolding and distributed the loads evenly along the whole scaffold structure.
It took six weeks to build the scaffold and install the elevators and four weeks to dismantle everything. Excel dismantled all of the scaffold while the splitter was running with no incident. Advantages and benefits of having the elevator and scaffold on the splitter included:
- Century’s elevators and Excel’s scaffold worked jointly to expedite installation and dismantling.
- Scaffold supported the equipment that assisted in controlling humidity levels and allowed for work during rainy weather.
- Multiple levels could be worked on at one time ultimately saving time off the outage and saving money.
- The scaffold decks provided protection to allow multiple projects being worked on at the same time.
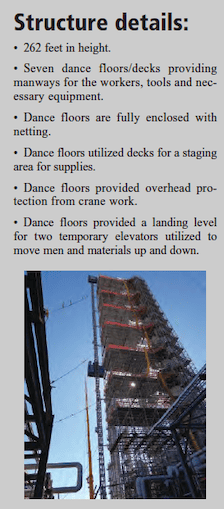
Century Elevators and Excel Modular Scaffold have worked together on past projects and the two companies have a solid relationship. Century has extensive experience attaching its elevators to scaffolding systems like the Excel system. “The engineering side of Excel is phenomenal,” said Gil Prado, regional sales manager of Century Elevators. “It’s easy to work with a company like Excel that knows what it’s doing and knows exactly what its capabilities are.” “Century is very responsive and they’re very knowledgeable about their products,” King said. “They have a newer product line, which was important for this project. Their elevators operate very smoothly putting less torque on the scaffold.
Safety
At Excel, the company promotes a safety culture that empowers all levels to engage and act as needed in regard to safety. Excel’s goal is zero incidents—anything less is unacceptable. “We executed this project while keeping safety as the No. 1 priority,” King said. “Everyone on this job performed efficiently and nobody got hurt.” Excel is dedicated to delivering a safe work environment where the focus rests on the prevention of incidents not only on the job but also away from work. Safety was also at the forefront when this structure was being built. A few of the many safety benefits associated with the Excel system include:
- Excel system requires fewer tools and repetitive motions when compared to other systems in the industry, which leads to less physical demands on the erectors.
- Excel system also affords a streamlined racking system, which reduces clutter and housekeeping issues while increasing productivity in a scaffold yard environment.
- Excel is one of the few systems in which the manufacturer has certified the system as an anchorage point to a majority of its horizontal bars.